Activity-Based Costing (ABC): Method and Advantages Defined with Example
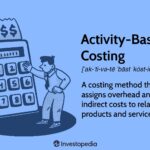
[ad_1]
What Is Activity-Based Costing (ABC)?
Activity-based costing (ABC) is a costing method that assigns overhead and indirect costs to related products and services. This accounting method of costing recognizes the relationship between costs, overhead activities, and manufactured products, assigning indirect costs to products less arbitrarily than traditional costing methods. However, some indirect costs, such as management and office staff salaries, are difficult to assign to a product.
Activity-Based Costing (ABC)
How Activity-Based Costing (ABC) Works
Activity-based costing (ABC) is mostly used in the manufacturing industry since it enhances the reliability of cost data, hence producing nearly true costs and better classifying the costs incurred by the company during its production process.
Key Takeaways
- Activity-based costing (ABC) is a method of assigning overhead and indirect costs—such as salaries and utilities—to products and services.
- The ABC system of cost accounting is based on activities, which are considered any event, unit of work, or task with a specific goal.
- An activity is a cost driver, such as purchase orders or machine setups.
- The cost driver rate, which is the cost pool total divided by cost driver, is used to calculate the amount of overhead and indirect costs related to a particular activity.
ABC is used to get a better grasp on costs, allowing companies to form a more appropriate pricing strategy.
This costing system is used in target costing, product costing, product line profitability analysis, customer profitability analysis, and service pricing. Activity-based costing is used to get a better grasp on costs, allowing companies to form a more appropriate pricing strategy.
The formula for activity-based costing is the cost pool total divided by cost driver, which yields the cost driver rate. The cost driver rate is used in activity-based costing to calculate the amount of overhead and indirect costs related to a particular activity.
The ABC calculation is as follows:
- Identify all the activities required to create the product.
- Divide the activities into cost pools, which includes all the individual costs related to an activity—such as manufacturing. Calculate the total overhead of each cost pool.
- Assign each cost pool activity cost drivers, such as hours or units.
- Calculate the cost driver rate by dividing the total overhead in each cost pool by the total cost drivers.
- Divide the total overhead of each cost pool by the total cost drivers to get the cost driver rate.
- Multiply the cost driver rate by the number of cost drivers.
As an activity-based costing example, consider Company ABC that has a $50,000 per year electricity bill. The number of labor hours has a direct impact on the electric bill. For the year, there were 2,500 labor hours worked, which in this example is the cost driver. Calculating the cost driver rate is done by dividing the $50,000 a year electric bill by the 2,500 hours, yielding a cost driver rate of $20. For Product XYZ, the company uses electricity for 10 hours. The overhead costs for the product are $200, or $20 times 10.
Activity-based costing benefits the costing process by expanding the number of cost pools that can be used to analyze overhead costs and by making indirect costs traceable to certain activities.
Activity-based costing benefits the costing process by expanding the number of cost pools that can be used to analyze overhead costs and by making indirect costs traceable to certain activities.
Requirements for Activity-Based Costing (ABC)
The ABC system of cost accounting is based on activities, which are any events, units of work, or tasks with a specific goal, such as setting up machines for production, designing products, distributing finished goods, or operating machines. Activities consume overhead resources and are considered cost objects.
Under the ABC system, an activity can also be considered as any transaction or event that is a cost driver. A cost driver, also known as an activity driver, is used to refer to an allocation base. Examples of cost drivers include machine setups, maintenance requests, consumed power, purchase orders, quality inspections, or production orders.
There are two categories of activity measures: transaction drivers, which involves counting how many times an activity occurs, and duration drivers, which measure how long an activity takes to complete.
Unlike traditional cost measurement systems that depend on volume count, such as machine hours and/or direct labor hours to allocate indirect or overhead costs to products, the ABC system classifies five broad levels of activity that are, to a certain extent, unrelated to how many units are produced. These levels include batch-level activity, unit-level activity, customer-level activity, organization-sustaining activity, and product-level activity.
Benefits of Activity-Based Costing (ABC)
Activity-based costing (ABC) enhances the costing process in three ways. First, it expands the number of cost pools that can be used to assemble overhead costs. Instead of accumulating all costs in one company-wide pool, it pools costs by activity.
Second, it creates new bases for assigning overhead costs to items such that costs are allocated based on the activities that generate costs instead of on volume measures, such as machine hours or direct labor costs.
Finally, ABC alters the nature of several indirect costs, making costs previously considered indirect—such as depreciation, utilities, or salaries—traceable to certain activities. Alternatively, ABC transfers overhead costs from high-volume products to low-volume products, raising the unit cost of low-volume products.
[ad_2]
Source link